|
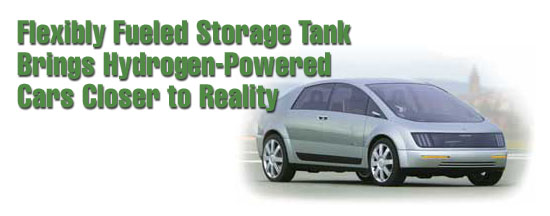
AS a Department of Energy national
laboratory, Livermore has long been involved in research and development
of alternative energy technologies for transportation, including
hydrogen fuel. Hydrogen-fueled passenger cars can have significant
advantages over todays or tomorrows gasoline cars. They
can eliminate automotive air pollution, reduce our nations
oil dependence, and reduce or eliminate greenhouse gas emissions
from transportation, if the hydrogen fuel is produced from nonfossil
energy resources.
But
as a recent article on the front page of the Wall Street Journal
(March 7, 2003) makes clear, hydrogen cars may be a long way off.
Numerous obstacles must be overcome before passenger cars using
hydrogen become a viable alternative to gasoline-powered vehicles.
Not the least of these is the development of extremely fuel-efficient
passenger cars. Be they fuel-cell vehicles or hybrid vehicles burning
hydrogen in an internal combustion engine, these cars must get the
equivalent of 60 to 100 miles per gallon (25 to 42 kilometers per
liter) and be capable of storing 5 kilograms of hydrogen onboard
to achieve a driving range of 300 to 500 miles (480 to 800 kilometers).
The worlds major automobile manufacturers are addressing this
challenge in a variety of hydrogen vehicle development programs.
Meeting the Storage Challenge
Other
obstacles to hydrogen cars fall into three large categories: hydrogen
production, refueling infrastructure, and hydrogen storage onboard
the vehicles. Researchers in Livermores Energy and Environment
Directorate have been addressing these problems for almost a decade.
(See S&TR, July
1995, This Hybrid Vehicle Uses Hydrogen; May
1997, The Unitized Regenerative Fuel Cell; December
1999, The Internal Combustion Engine at Work.) Recently, a team
in Energy and Environments Energy Technology and Security
Program has turned its attention to the challenges of storing hydrogen
fuel onboard automobiles. Led by engineer Salvador Aceves, associate
program leader for transportation, the group has designed and tested
a safe and compact system for on-vehicle storage of hydrogen fuel.
The tank, which shows great promise, was featured on the cover of
the February 2002 issue of Mechanical Engineering and will
soon be installed on test vehicles.
The beauty of the Livermore tank, says Aceves, is that it can safely
and simultaneously accommodate three forms of hydrogen fuelconventional
high-pressure hydrogen gas, cryogenic compressed gaseous hydrogen,
and liquid hydrogen. And it does so while minimizing the storage
challenges and maximizing the energy efficiency potential of each.
|
The
Livermore hydrogen fuel storage tank has two basic parts:
(a) a composite-coated interior pressure vessel wrapped with
80 layers of Mylar insulation and (b) an exterior stainless-steel
pressure vessel. The vacuum induced between the two vessels
minimizes the heat transfer that causes cryogenic hydrogen
to evaporate. |
Three Fuel Forms, One Tank
Similar
to compressed natural gas vehicles, prototype hydrogen vehicles
use compressed hydrogen, stored onboard at about room temperature
and under moderate pressure (25 to 35 megapascals). Unfortunately,
these moderate pressures lead to large fuel tanks and/or limited
driving range because the energy density of simple hydrogen molecules
(H2) is lower than the energy density of conventional fossil fuels
such as gasoline (C8H18) or natural gas (CH4), both of which are
more complex molecules. One kilogram of hydrogen gas at 25 megapascals
occupies nearly 60 liters (16 gallons), but its energy (33.3 kilowatt-hours)
is equivalent to just 1 gallon of gasoline. Compressed hydrogen
is a simpler, less costly, and more energy-efficient method of storage
than other methods and is well suited for the range of the majority
of urban drivers in the U.S.: 150 to 200 miles.
Since
all gases occupy less volume at colder temperatures, compressed
hydrogen can be stored more compactly when cryogenically cooled.
At temperatures of 80 kelvins (193°C), near the boiling
point of liquid nitrogen, 60 liters of hydrogen gas at 25 megapascals
contains the energy equivalent to more than 3.3 gallons of gasoline,
enabling cars using cryogenic hydrogen to greatly extend their driving
range.
Liquid
hydrogen is even more compact than cryogenic hydrogen, but because
hydrogens boiling point (20 kelvins) is lower than that
of any substance except helium, liquefying hydrogen is complicated
and not energy efficient. Typically, 11 to 12 kilowatt-hours of
electricity are needed to produce 1 kilogram of liquid hydrogen,
which contains only 33.3 kilowatt-hours of fuel energy. This high
energy penalty is a key factor in the high production cost of liquid
hydrogen.
Liquid
hydrogen has its advantages, however. It is relatively easy and
safe to store and transport in compact, lightweight, low-pressure
containers. According to project engineer Gene Berry, a hydrogen
car designed to get the equivalent of 60 miles per gallon of gasoline
uses 100 liters of liquid hydrogen to travel 420 miles, compared
to 240 miles on high-pressure (70 megapascals) compressed hydrogen
and 140 miles on moderate-pressure (35 megapascals) compressed
hydrogen. Liquid hydrogen is thus ideal for long highway trips.
Its advantages help explain why it has become the favorite of BMWs
20-year hydrogen vehicle development program.
The
rub is that liquid hydrogen is extremely sensitive to heat, expanding
significantly when warmed only a few degrees. When a hydrogen-fueled
car is not being driven, heat exchange between the storage tank
and the outside environment warms the fuel, causing it to evaporate.
As the hydrogen fuel expands, the pressure in the tank increases.
The hydrogen must therefore be vented to the atmosphere to prevent
the dangerous buildup of excessive pressure.
Cryogenic
hydrogen fuel in a standard liquid hydrogen tank typically warms
up enough in 3 to 4 days after refueling to require venting. The
tank team used computer analysis to determine that when liquid hydrogen
is stored in a conventional low-pressure (0.5-megapascal) tank in
a car that gets the equivalent of 80 miles per gallon, it would
begin to vent and lose fuel if driven (on average) less than about
15 miles daily. Evaporation losses increase sharply if the car is
driven less. In a parked car, an entire tank of liquid hydrogen
fuel will completely evaporate in just 3 weeks. Eliminating this
evaporation is a primary goal of Livermores tank design.
Insulation in a Vacuum to the Rescue
To date, conventional cryogenic hydrogen storage vessels could accommodate
only low-pressure liquid hydrogen. By insulating conventional high-pressure
vessels, the Laboratorys team designed a tank that successfully
combines cryogenics and high pressure to allow three forms of hydrogen
to be stored in one tank. Aceves and his team determined that commercially
available aluminum-lined pressure vessels coated with composites
(Aramid or carbon fiber) identical to those popular for natural
gas storage offered the low weight and affordability desired for
automotive fuel storage. The researchers coated a standard pressure
vessel with 80 layers of highly reflective, metallized Mylar and
then enclosed and sealed the insulated inner vessel in a stainless-steel
outer tank. A vacuum is then created between the inner and outer
tank. Heat transfer, which is the culprit for evaporation
loss, operates through convection, conduction, and radiation,
says Aceves. The vacuum created between the two tanks eliminates
the convection and conduction that would otherwise have occurred
with a standard tank. The multiple layers of reflective material
considerably reduce heat transfer by radiation.
The researchers built openings in the outer jacket for thermocouples,
strain gauges, and a capacitive level sensor to measure pressure,
temperature, and the fuel level within the test tank. They equipped
the tank with safety devices to prevent catastrophic failure in
case hydrogen leaked into the vacuum area. Relief valves open if
the pressure limits are exceeded, and if the relief valves fail,
rupture disks prevent explosive pressure release.
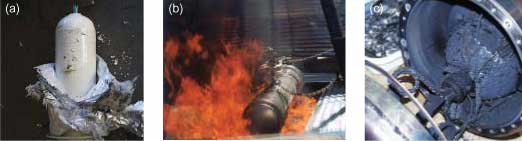
|
Livermore’s
insulated cryogenic hydrogen tank has undergone 27 different
tests to demonstrate its safety and reliability. (a) The
tank after being shot with a .30-caliber armor-piercing bullet.
The bullet punctured the tank without fragmenting it. (b)
The Livermore tank during the bonfire test and (c) following
the test. The tank was charred but retained its structural
integrity, a key safety consideration. |
Putting the Tanks to the Test
To
determine if the Livermore-designed tank meets rigorous U.S.
Department of
Transportation and Society of Automotive Engineers safety standards,
the researchers constructed tanks to one-fifth scale and subjected
them to 27 tests of materials, construction, and performance.
Many
tests involved thousands of repetitions, or cycles. For example,
to determine whether the tanks can withstand severe and repeated
pressure changes at extremes of internal temperature, the tanks
were pressurized from zero to full-service pressure (25 megapascals)
and then returned to zero. The cycle was repeated 5,000 times, about
5 times the number of cycles that a typical tank will experience
over a 150,000-mile vehicle lifetime. The cycles were first done
with an internal tank temperature of 140°F and external ambient
air temperatures at 95-percent humidity and then repeated with an
internal tank temperature of 60°F and external high-humidity
ambient temperatures. The tanks were also subjected to 20 thermal
cycles, with tank temperatures ranging from 200°F to 60°F
at full-service pressure.
Some
of the more dramatic tests included dropping tanks 3 meters onto
a hard surface, firing a .30-caliber armor-piercing bullet at a
tank from 15 meters, and placing pressurized tanks in bonfires.
The tanks survived or suffered acceptable damage. The tank was pierced
by the bullet but did not fragment, and it was charred by the fire
but retained its structural integrity and did not explode.
The
tank design passed all of these tests and met all of the standards.
In some instances, the tanks exceeded the testing criteriaand
the teams expectationsespecially for cryogenic storage.
When the tests showed that the cryogenic tanks were at least
as strong as conventional tanks, people sat up and took notice.
says Berry. Suddenly, the Livermore concept was considered
a viable option for storing hydrogen on cars of the future.
Now Comes the Real Test
The next step for the Livermore researchers is installing their
insulated cryogenic pressure vessels on vehicles for field testing.
They are now working on a second-generation tank, which will hold
9 kilograms of liquid hydrogen, energy equivalent to 9 gallons of
gasoline. They are working with two partners in getting their tanks
on the road: Structural Composites Industries, a leading manufacturer
of pressure vessels based in Pomona, California, and Sunline Transit
of Thousand Palms, California. Sunline, a mass transit agency serving
the Palm Springs area, has agreed to install two second-generation
Livermore tanks on pickup trucks. One truck will carry hydrogen,
and the other will carry natural gas.
If the second-generation tank is successful, the Livermore team
will give the design what many consider the real test: subjecting
these tanks to continual, daily use. In these days of high gasoline
prices and increasing concerns about air pollution and global warming,
on-road testing of the Livermore hydrogen fuel tank is one small
step of a long journey.
Laurie Powers
Acknowledgments: Members of the project team responsible for the
work reported in this article are Salvador Aceves, Gene Berry, Francisco
Espinosa, Timothy Ford, James Fugina, Joel Martinez, Timothy Ross,
and Vernon Switzer.
Key Words: compressed hydrogen, cryogenic compressed hydrogen, hydrogen
fuel, liquid hydrogen.
For further information contact Salvador Aceves (925) 422-0864
(aceves6@llnl.gov).
Download a printer-friendly
version of this article.
|